Table of Contents
Introduction:
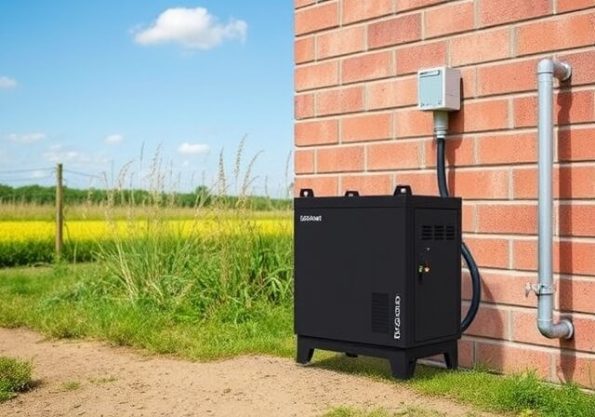
It is mandatory to have good energy storage if one has to begin with utilizing more of renewable energy, which in some situations is unavoidable. The latest entrant into the market is the lithium battery for inverter. It means that they are changing how we supply power in households and other commercial establishments. And they’re getting popular fast! Alright then it would have been useful to get seven thrilling exhaustive ways that would provide a alters in lithium battery for inverter.
1. Enhancement of The Lifespan and Endurance of Lithium Battery of Inverters
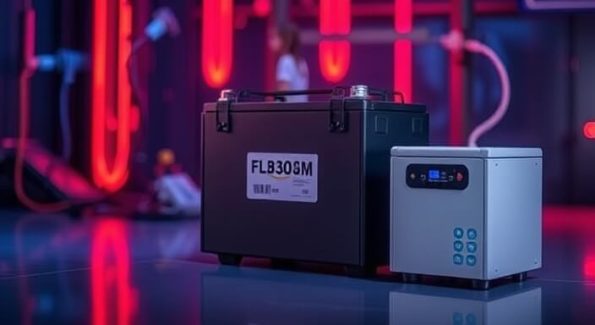
This is why long cycle life one of the most important performance to any energy storage in the modern world. On this foundation, current favorite batteries include the 12V lithium ion battery or 200Ah lithium ion battery because they can outlast the more established lead-acid batteries on the market. Inverter lithium battery has a lifespan of about 10 to 15 years; however, inverter lead-acid batteries for home only last for 3 to 5 years only. This makes them a wise investment to homeowners because they provide the long term solution that will aid in energy storage.
Lithium-ion batteries self-discharge more slowly, which, for the record, is a lesser flaw than that of rapidly self-discharging NiMH batteries and degrading from a much higher capacity than a NiMH battery and in much smaller increments. This ensures that your inverter system has longevity and that you can store as much clean energy as you want for use later without having to put in for a new one.
2. In a higher level, efficiency of power storage
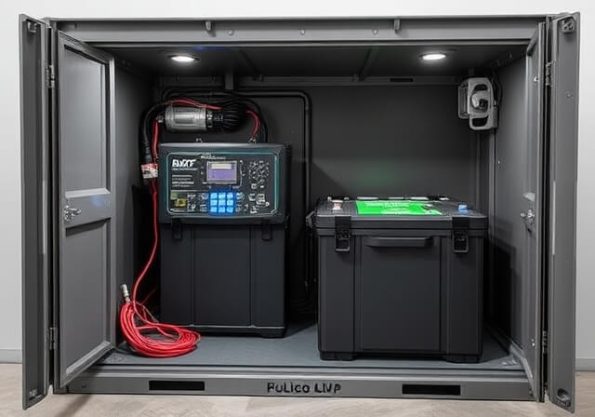
Besides that, lithium-ion batteries for inverter are far more efficient compared with the other kinds of batteries. As mentioned earlier, Lithium ion batteries contain an efficiency of up to 95 % and therefore the energy harnessed is useful in powering the appliances. They should be made especially when you are using an inverter to supply power that can be used from solar power or other sources of renewable power.
Lithium battery for inverter systems also self-charge and self-discharge more quickly and uniformly and therefore well suited for both high end power consumption as well as low end power consumption application. Whereas, in lithium batteries there is a conversion loss; in combustion lead-acid batteries, some amount of energy loss happens during charge discharge cycles; you get somewhat less usable energy.
3. Portability Integrated in that it is light and thus occupies a neat and little built space.
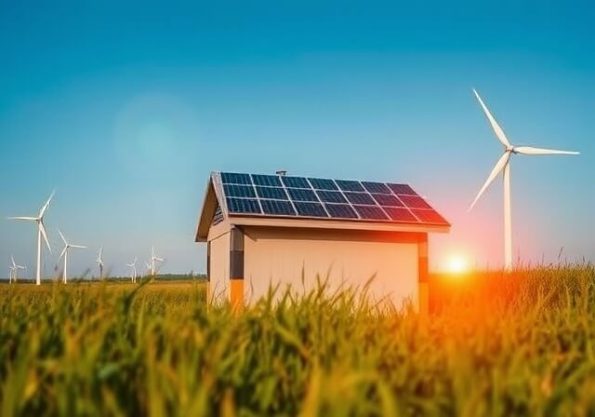
Third, lithium-ion batteries offer a portability and small size dimensions of the batteries as other benefits. Lead-acid batteries are normally used in UPS systems; however, conventional ones can be physically large, and therefore can be somewhat cumbersome to mount especially if the UPS is to be situated in an area where space is limited. Nevertheless, 12V lithium-ion battery and 200ah lithium-ion battery allow for more energy-storage capacity in even less mass. They are also easier to mobilize, to construct and to maintain than the field constructed steel ones such as.
Thus if you need a battery to fit a home or office use inverter you will notice the slim profile on a lithium ion battery.
4. But, most importantly, it costs much less than most methods in the long run.
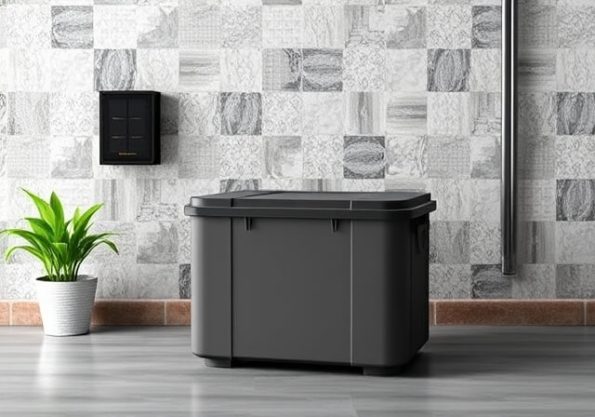
The Lithium-ion types of batteries have obvious higher initial cost per power unit than the traditional types However, the fact that must be noted is that in the long run the lithium-ion battery is self funded. Lithium-ion battery for inverter have relatively long life cycles and only need to be replaced when the others have finally given up. This translates to attaining the goals of lowering replacement cost, maintaining and therefore a better solution is cheaper.
Secondly, lithium batteries in inverters are many times more efficient in terms of charging and discharging rates so you are not eating up your energy. As time goes this can be very cost effective because you are cutting down your electricity bills if the energy used has been extracted from the sun or any natural source.
5. Faster Charging Times
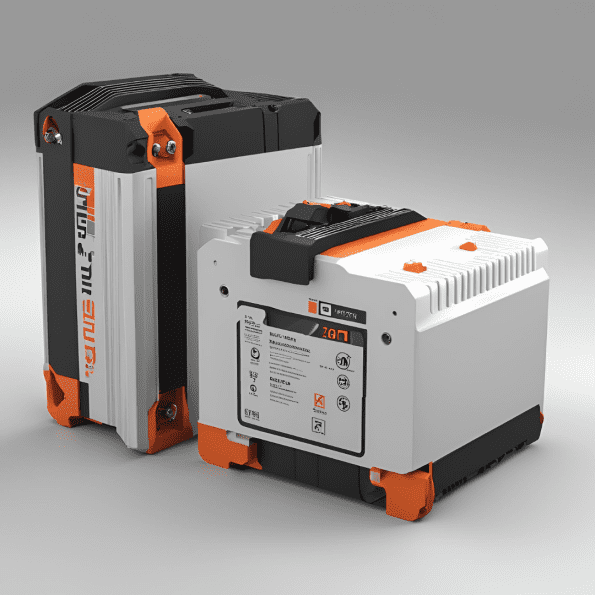
The third benefit Lithium-ion batteries offer inverters is that they are rechargeable at a rate faster than one would achieve with lead-acid batteries. A 12V lithium-ion battery will charge 2-3 time faster than a traditional lead-acid battery making it suitable for home use where there are times that you will need to recharge the batteries in a day without a direct sunshine. A charging function one that is faster makes lithium batteries even more ideal for those who use solar inverters.
6. The issues of sustainable energy resource have also been discussed in the context of the proposed solution dubbed an Eco-friendly solution.
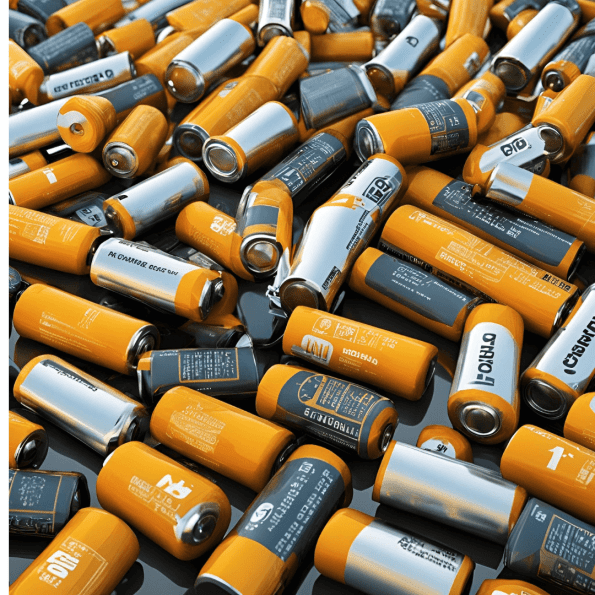
However, one must not fail to note that Li-ion batteries cost the environment a better bargain than conventional lead-acid batteries. Compared to other product forms, its production involves minimal use of raw materials and produces minimal waste. Third, FMCVs can be recycled easier; actually, the parts of FMCVs can be easier to recycle in comparison with B Nationwide, because most of the parts are standardized and interchangeable. Due to the popularity of the renewable energy sources, most of the home owners need to store power and lithium battery for inverter systems is used in this purpose.
We are in fact improving efficiency and availability of the energy system that exists here with conventional lithium-ion batteries, and in so doing are gaining big leaps for a better world.
7. Scalability for Future Needs
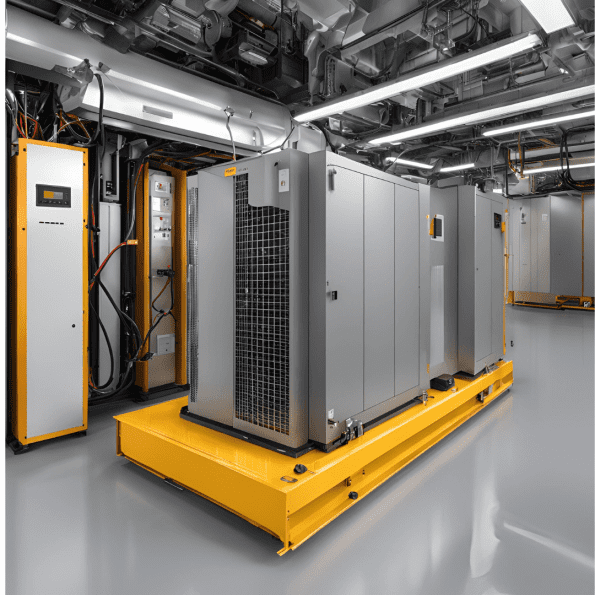
But the primary reason as energy demands rise, lithium-ion battery for inverter application has to be scalable in terms of capacity. Lithium ion batteries and including the 200Ah lithium ion battery make it simple to extend the energy storage system of a certain capacity. The system also allows for the addition of more batteries should your energy demands increase over time, without much effect on the system.
This scalability assure that your energy storage solution is capable of expansion according to the future advancement in technology or increased consumption of electricity.
Conclusion
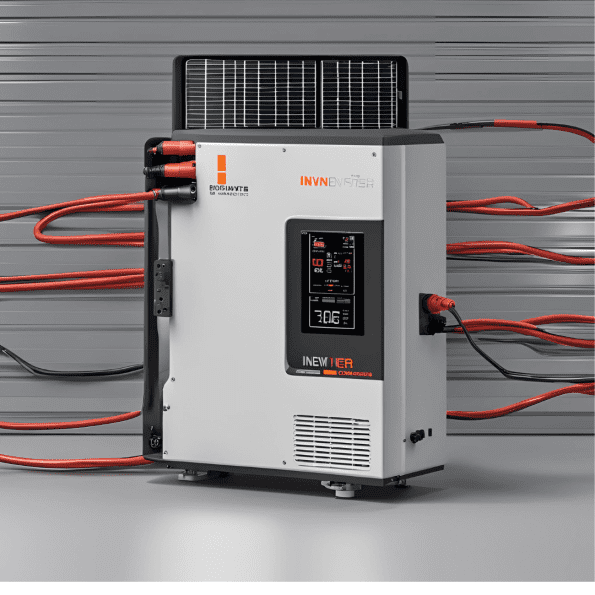
Consequently, the decision of the battery to use with the inverter then goes back to lithium battery for inverter for anyone wishing to spend appropriate money and efforts on long-term energy storage. From a longer service life and higher efficiency to compact size and lower costs lithium-ion batteries are much more favourable than standard lead-acid batteries.
If you are making plans of investing in a new energy storage system, it will be most appropriate to invest in a 12V lithium ion battery or better still Lithium ion battery 200Ah that you will be using in your inverter. Such batteries offer reliability of power supply each and at the same time guarantee clean and sustainable electricity provision. Switch now and you get to see the gain on enhancing the energy on your home.
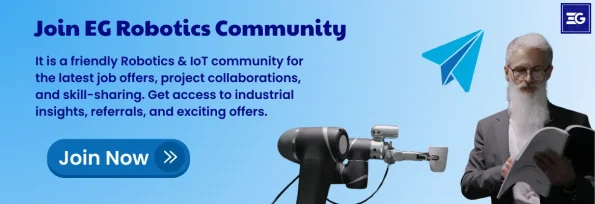
Q1- Two lithium ion batteries ?
Ans- When two lithium-ion batteries are connected with each other some important concern is related to the wire connection and the protection circuit to avoid over charging, short circuit or damage lithium-ion battery. There are two common ways to connect them: in series and in parallel. Here’s how you can do each:
- Connecting Lithium-Ion Batteries in Series:
Lithium-ion batteries can be connected in series or objects and in parallel We can connect two lithium-ion batteries in series, in such case, the voltage would be added or doubled while the Ah or mAh capacity would stay the same.
Steps:
Check the Battery Voltage and Capacity:
It is desirable that the two batteries have the same voltage (for example 3,7V) and the same capacity (for example 2500mAH).
Never put batteries of different voltage or capacity in series because it will develop issues that will harm the batteries.
Wiring the Batteries:
The last terminal is the positive terminal of the second battery as an output while the rest of the negative terminal of the first battery as the output.
Balancing Circuit (Important!):
In arranged connection, ensure that you use a Battery management system (BMS) in order to continuously measure the voltage of every battery, and ensure they are well balanced.
A BMS is important for preventing either from overcharging or deep discharging dangerous to the batteries in question.
Safety Precautions:
It important to always use a proper BMS or charge controller when connecting the batteries in series especially if they are lithium-ion batteries.
Remember that batteries connected together should be of similar voltage and should ideally be as charged or as discharged as one another possible.
Employ this one if there is need for conditions like over current voltage.
Q2- Why lithium ion batteries are so expensive?
Ans- Li-ion batteries are much more costly due to raw materials required, high technology integration while constructing, and due to complexity. Here are the main factors that contribute to their high price:
- Cost of Raw Materials:
Lithium: Lithium the raw material which is used in these batteries is in limited supply and cost prohibitive. Extraction of sp porn lithium from deposits or brines involves more complex and expensive process, technique or technology.
Cobalt: Another expensive component is cobalt used as an additive in a lithium-ion cathode material to boost energy density as well as the cyclic stability of the cathode material. Cobalt is relatively rare and, to add, its extraction involves environmental and ethical costs which raise the final price.
Nickel and Manganese: The third material in common use in lithium-ion batteries is nickel. Nickel prices vary depending on requests of industries namely electric vehicles in return regulating battery price in the market.
- Manufacturing Complexity:
Sophisticated Production Process: The industrial production of lithium-ion battery involves high accuracy and complex technology of production. Battery cell orientation is a safety concern and also plays a role in power distribution of the cells and their longevity. It involves the use of an anode, cathode, electrolyte and separator and all these components might need the most elaborate manufacturing process involving specialized equipment and test results.
Scale of Production: Therefore, while the major costs associated with lithium-ion batteries have become less because of scale advantages, the manufacturing of lithium-ion batteries is still on a smaller scale than that of the other battery products such as the alkaline batteries. The overall production capacity for high performance cells still remains limited and so does the manufacturing cost.
- Battery Management Systems (BMS):
No Li-ion battery is allowed to operate without battery management system (BMS) in order to function properly and safely. BMS track the voltage and the temperature, charge and discharge currents and also stops overcharging, overheating and deep discharge of battery. These systems are not only necessary for safe battery operation but also lead to cost escalation of the battery pack.
- Research and Development (R&D):
A considerable amount of investment is made towards the advancement of lithium-ion batteries in terms of energy density, cycle life, charging capabilities and safety of the battery; new players such as solid state battery or cathode/anode material are under development. Hitherto expenses such as research and development costs are performed relatively by the client while they are over reimbursing the cost of the product.
- Safety Considerations:
Safety Features: For lithium-ion batteries, additional layers of safety must be provided to prevent such issues as thermal runway which is fire/explosion, particularly at high energy user end devices such as EVs. Subcomponents of battery pack like flame retardants, separators, and protectors establish additional costs of battery packs.
Quality Control: Since bad batteries can be very dangerous with potential for overheating and even catching fire, better or best tests, good quality control plus certification also contribute to the manufacturing cost.
- Demand for High-Performance Batteries:
Demand for lithium-ion batteries is high thanks to an ever-growing need for electric vehicles – it covers consumer products like smartphones and laptops – and other large-scale applications, including the storage of renewable energy from sources such as solar and wind power. This demand endangers supplies which alters the nature of cost of raw materials and makes new innovations costly to manufacture.
The need for higher life expectancy and increase of the density of the batteries’ energy requires better and costly production technologies.
- Environmental and Ethical Costs:
Lithium, cobalt and nickel used in electrolytes here are primarily from countries with little or no regard for environmental or indeed ethical consequences. This strategy means improving the quality of working conditions for people and minimizing such a negative effect on the environment which, in turn, may further the costs of producing goods and services.
- Logistics and Supply Chain:
Lithium-ion batteries are dangerous and as such their transportation is costly because they need special precautions. Also, events that happened in the present period like a rise in the cost of raw material due to political unrest between trading partners or internationally imposed ban on certain material will help to push cost up.
Conclusion:
Hence, costs associated with the production of lithium-ion batteries have some causes such as high cost of the materials used, process of making the batteries, safety measurement, and production enhancement. While these costs are actually decreasing with time as the technology advances, and as the effects of economies of scale come to realization, LIBs are nonetheless a significant expense based on the identified factors above.
Q3- How lithium ion battery is made ?
Ans- There is need to understand this and also need facilities and equipment and of course follow certain measures of precaution when manufacturing a lithium-ion (Li-ion) battery. It is not an area that could be done from home as it involves using dangerous chemicals, high voltage and accuracy in manufacturing. Unfortunately, I mentioned before, I did not focus much on the creation of this model and thus was not able to make a good progress, but still in the creation of this model, there are some basic steps as follows. Here’s a simplified overview of how lithium-ion batteries are typically made:
Materials Required:
Anode Material: More frequently than not some form of graphite or other variations of the fourth element, which is carbon.
Cathode Material: In general the lithium metal oxide (Lithium Cobalt oxide, lithium iron phosphate or Lithium nickel manganese cobalt oxide).
Electrolyte: An organic solvent solution containing a lithium salt such as, lithium hexafluorophosphate.
Separator: A non-metal matrix (may include polyethylene and polypropylene), so an electrode known as an anode cannot come into contact with the other known as the cathode, but the ions can pass through it.
Current Collectors: The cathode is required to be of aluminum and vice versa the anode should be of copper.
Steps in Manufacturing a Lithium-Ion Battery:
- Preparation of the Electrodes:
Anode (Negative Electrode): The anode being used in the Li ion battery is predominantly sourced from graphite material. Graphite powder is converted to a paste with a binder; polyvinylidene fluoride, PVDF and solvent, N-Methyl-2-pyrrolidone, NMP. For formation of the anode electrode, this paste is installed and coated on copper foil.
Cathode (Positive Electrode): All that said about the anode production could be equally said about the cathode material which could be lithium cobalt oxide (LiCoO₂) or lithium iron phosphate (LiFePO₄). After that, it is coated on an aluminum foil which in this battery device is used as the current collector of the cathode part.
- Drying and Compression:
In the other case, the anode and cathode materials are eliminate solvent that may be present since they are dried.
The electrodes are then conditioned at comparatively high temperatures to remove as much moisture as possible and then pressing is performed to ensure that they are of the required thickness and pore size to enable ions to transfer bidirectional through charging and discharging cycles.
- Cutting and Shaping:
Last of all after drying and the electrodes are compressed they are cut into the required thickness often circular or rectangular using a slitting machine to match the appearance of the battery to be produced.
- Assembly of the Cell:
There is another flat anode and cathode electrodes which are sealed by very thin layer called as the separator; the best separator should not allow the electrodes to come close to each other but the lithium ions can come in between.
The anode, separator and cathode layers are rolled or coiled in the shape of a jelly roll for cylinder type while one above the other in pouch or prismatic type. This separator does away with any danger of shorting of the anode with the cathode by the flow of electricity .
The rolled or stacked assembly is then placed within a battery casing, the construction of which may differ; nevertheless most are constructed from metal for cylindrical or prismatic cell designs or are a pouch design for pouch cell design.
- Electrolyte Injection:
The battery is then charged with a liquid electrolyte: this is lithium salt which has been dissolved in an organic solvent. This electrolyte will allow the lithium ions to shuttle between the anode and the cathode during the charging, and the discharging.
The electrolyte is then put into the cell and the connection is established such that the particular points of the cell are airtight and gulled.
- Formation and Initial Charging:
After assembly, another calendar process for the battery is carried out for the charging and discharging of electrodes for activation of the electrodes and to form a stable layer of SEI on anode.
At this process constant monitoring is required in order not to overheat the cell and to make sure that the cell becomes unstable.
- Testing and Quality Control:
Each battery is subjected to voltage test, capacity test, internal resistance test, and safety tests as well. Because of this, they are examined to determine if they meet certain provision on performance and security.
The batteries are tested under charge/ discharge cycling, over charging, and short circuit testing methods which afford the needed guarantee with regard to the batteries reliability and safety whenever they are in use.
- Packaging:
The cells are tested and if required are placed into the battery pack of the vehicle. For example, in case of EVs or energy storage systems, cells are grouped in packs For instance, a single cell to constitute the pack. The above packs can maybe contain BMS for tracking performance of the packs as observed by.
Q4- What products use lithium ion batteries ?
Ans- Lithium ion batteries are used in all electronics such as smartphones, laptops, electric cars, power tools, drones, medical equipment and much more. They are also employed in renewable energy storage and backup power applications and also in industrial products such as robotics equipment. The end products are characterized by high energy density and promptness of operations and are widely used in various electronic gadgets, automobiles and energy storage.
Q5- How to increase lithium ion battery life ?
Ans- Do not discharge lithium-ion batteries to zero percent and charge them fully to maximize battery durability, use charge level between 20-80%. Using the original charger and do not charge the headphone for a longer period of time. Charge the battery at the right temperature – away from heat and sun exposure. Do not use it where high band width or high performance demands are required. If devices are not in use for long time, they should be charged to around 50% and the firmware of the device should be updated frequently.
Q6 Do laptops use lithium ion batteries ?
Ans- Indeed, majority of current laptops have lithium-ion battery as this type has high energy density per unit weight, fairly durable. These batteries offer power delivery, convenience of charge, and higher utilization time which makes these appealing for power driven items like pills. Some newer models even use lithium-polymer batteries, a variation of the lithium-ion technology and thinner than the other three models.
Q7- How is lithium ion battery manufactured ?
Ans- Lithium-ion batteries have electrodes where cathodes – compounds with lithium – are coated on aluminum foil and anodes – graphite – coated on copper foil and they are separated by a layer of a porous material. The assembly is filled with a lithium-ion electrolyte, sealed, and further the assembly is subjected to the first cycle of charging which is known as formation. The primary purpose of quality control is to guarantee both performance, safety as well as reliability in the end product.
Ans- When two lithium-ion batteries are connected with each other some important concern is related to the wire connection and the protection circuit to avoid over charging, short circuit or damage lithium-ion battery. There are two common ways to connect them: in series and in parallel. Here’s how you can do each:
- Connecting Lithium-Ion Batteries in Series:
Lithium-ion batteries can be connected in series or objects and in parallel We can connect two lithium-ion batteries in series, in such case, the voltage would be added or doubled while the Ah or mAh capacity would stay the same.
Steps:
Check the Battery Voltage and Capacity:
It is desirable that the two batteries have the same voltage (for example 3,7V) and the same capacity (for example 2500mAH).
Never put batteries of different voltage or capacity in series because it will develop issues that will harm the batteries.
Wiring the Batteries:
The last terminal is the positive terminal of the second battery as an output while the rest of the negative terminal of the first battery as the output.
Balancing Circuit (Important!):
In arranged connection, ensure that you use a Battery management system (BMS) in order to continuously measure the voltage of every battery, and ensure they are well balanced.
A BMS is important for preventing either from overcharging or deep discharging dangerous to the batteries in question.
Safety Precautions:
It important to always use a proper BMS or charge controller when connecting the batteries in series especially if they are lithium-ion batteries.
Remember that batteries connected together should be of similar voltage and should ideally be as charged or as discharged as one another possible.
Employ this one if there is need for conditions like over current voltage.
Ans- Li-ion batteries are much more costly due to raw materials required, high technology integration while constructing, and due to complexity. Here are the main factors that contribute to their high price:
- Cost of Raw Materials:
Lithium: Lithium the raw material which is used in these batteries is in limited supply and cost prohibitive. Extraction of sp porn lithium from deposits or brines involves more complex and expensive process, technique or technology.
Cobalt: Another expensive component is cobalt used as an additive in a lithium-ion cathode material to boost energy density as well as the cyclic stability of the cathode material. Cobalt is relatively rare and, to add, its extraction involves environmental and ethical costs which raise the final price.
Nickel and Manganese: The third material in common use in lithium-ion batteries is nickel. Nickel prices vary depending on requests of industries namely electric vehicles in return regulating battery price in the market.
- Manufacturing Complexity:
Sophisticated Production Process: The industrial production of lithium-ion battery involves high accuracy and complex technology of production. Battery cell orientation is a safety concern and also plays a role in power distribution of the cells and their longevity. It involves the use of an anode, cathode, electrolyte and separator and all these components might need the most elaborate manufacturing process involving specialized equipment and test results.
Scale of Production: Therefore, while the major costs associated with lithium-ion batteries have become less because of scale advantages, the manufacturing of lithium-ion batteries is still on a smaller scale than that of the other battery products such as the alkaline batteries. The overall production capacity for high performance cells still remains limited and so does the manufacturing cost.
- Battery Management Systems (BMS):
No Li-ion battery is allowed to operate without battery management system (BMS) in order to function properly and safely. BMS track the voltage and the temperature, charge and discharge currents and also stops overcharging, overheating and deep discharge of battery. These systems are not only necessary for safe battery operation but also lead to cost escalation of the battery pack.
- Research and Development (R&D):
A considerable amount of investment is made towards the advancement of lithium-ion batteries in terms of energy density, cycle life, charging capabilities and safety of the battery; new players such as solid state battery or cathode/anode material are under development. Hitherto expenses such as research and development costs are performed relatively by the client while they are over reimbursing the cost of the product.
- Safety Considerations:
Safety Features: For lithium-ion batteries, additional layers of safety must be provided to prevent such issues as thermal runway which is fire/explosion, particularly at high energy user end devices such as EVs. Subcomponents of battery pack like flame retardants, separators, and protectors establish additional costs of battery packs.
Quality Control: Since bad batteries can be very dangerous with potential for overheating and even catching fire, better or best tests, good quality control plus certification also contribute to the manufacturing cost.
- Demand for High-Performance Batteries:
Demand for lithium-ion batteries is high thanks to an ever-growing need for electric vehicles – it covers consumer products like smartphones and laptops – and other large-scale applications, including the storage of renewable energy from sources such as solar and wind power. This demand endangers supplies which alters the nature of cost of raw materials and makes new innovations costly to manufacture.
The need for higher life expectancy and increase of the density of the batteries’ energy requires better and costly production technologies.
- Environmental and Ethical Costs:
Lithium, cobalt and nickel used in electrolytes here are primarily from countries with little or no regard for environmental or indeed ethical consequences. This strategy means improving the quality of working conditions for people and minimizing such a negative effect on the environment which, in turn, may further the costs of producing goods and services.
- Logistics and Supply Chain:
Lithium-ion batteries are dangerous and as such their transportation is costly because they need special precautions. Also, events that happened in the present period like a rise in the cost of raw material due to political unrest between trading partners or internationally imposed ban on certain material will help to push cost up.
Conclusion:
Hence, costs associated with the production of lithium-ion batteries have some causes such as high cost of the materials used, process of making the batteries, safety measurement, and production enhancement. While these costs are actually decreasing with time as the technology advances, and as the effects of economies of scale come to realization, LIBs are nonetheless a significant expense based on the identified factors above.
Ans- There is need to understand this and also need facilities and equipment and of course follow certain measures of precaution when manufacturing a lithium-ion (Li-ion) battery. It is not an area that could be done from home as it involves using dangerous chemicals, high voltage and accuracy in manufacturing. Unfortunately, I mentioned before, I did not focus much on the creation of this model and thus was not able to make a good progress, but still in the creation of this model, there are some basic steps as follows. Here’s a simplified overview of how lithium-ion batteries are typically made:
Materials Required:
Anode Material: More frequently than not some form of graphite or other variations of the fourth element, which is carbon.
Cathode Material: In general the lithium metal oxide (Lithium Cobalt oxide, lithium iron phosphate or Lithium nickel manganese cobalt oxide).
Electrolyte: An organic solvent solution containing a lithium salt such as, lithium hexafluorophosphate.
Separator: A non-metal matrix (may include polyethylene and polypropylene), so an electrode known as an anode cannot come into contact with the other known as the cathode, but the ions can pass through it.
Current Collectors: The cathode is required to be of aluminum and vice versa the anode should be of copper.
Steps in Manufacturing a Lithium-Ion Battery:
- Preparation of the Electrodes:
Anode (Negative Electrode): The anode being used in the Li ion battery is predominantly sourced from graphite material. Graphite powder is converted to a paste with a binder; polyvinylidene fluoride, PVDF and solvent, N-Methyl-2-pyrrolidone, NMP. For formation of the anode electrode, this paste is installed and coated on copper foil.
Cathode (Positive Electrode): All that said about the anode production could be equally said about the cathode material which could be lithium cobalt oxide (LiCoO₂) or lithium iron phosphate (LiFePO₄). After that, it is coated on an aluminum foil which in this battery device is used as the current collector of the cathode part.
- Drying and Compression:
In the other case, the anode and cathode materials are eliminate solvent that may be present since they are dried.
The electrodes are then conditioned at comparatively high temperatures to remove as much moisture as possible and then pressing is performed to ensure that they are of the required thickness and pore size to enable ions to transfer bidirectional through charging and discharging cycles.
- Cutting and Shaping:
Last of all after drying and the electrodes are compressed they are cut into the required thickness often circular or rectangular using a slitting machine to match the appearance of the battery to be produced.
- Assembly of the Cell:
There is another flat anode and cathode electrodes which are sealed by very thin layer called as the separator; the best separator should not allow the electrodes to come close to each other but the lithium ions can come in between.
The anode, separator and cathode layers are rolled or coiled in the shape of a jelly roll for cylinder type while one above the other in pouch or prismatic type. This separator does away with any danger of shorting of the anode with the cathode by the flow of electricity .
The rolled or stacked assembly is then placed within a battery casing, the construction of which may differ; nevertheless most are constructed from metal for cylindrical or prismatic cell designs or are a pouch design for pouch cell design.
- Electrolyte Injection:
The battery is then charged with a liquid electrolyte: this is lithium salt which has been dissolved in an organic solvent. This electrolyte will allow the lithium ions to shuttle between the anode and the cathode during the charging, and the discharging.
The electrolyte is then put into the cell and the connection is established such that the particular points of the cell are airtight and gulled.
- Formation and Initial Charging:
After assembly, another calendar process for the battery is carried out for the charging and discharging of electrodes for activation of the electrodes and to form a stable layer of SEI on anode.
At this process constant monitoring is required in order not to overheat the cell and to make sure that the cell becomes unstable.
- Testing and Quality Control:
Each battery is subjected to voltage test, capacity test, internal resistance test, and safety tests as well. Because of this, they are examined to determine if they meet certain provision on performance and security.
The batteries are tested under charge/ discharge cycling, over charging, and short circuit testing methods which afford the needed guarantee with regard to the batteries reliability and safety whenever they are in use.
- Packaging:
The cells are tested and if required are placed into the battery pack of the vehicle. For example, in case of EVs or energy storage systems, cells are grouped in packs For instance, a single cell to constitute the pack. The above packs can maybe contain BMS for tracking performance of the packs as observed by.
Ans- Lithium ion batteries are used in all electronics such as smartphones, laptops, electric cars, power tools, drones, medical equipment and much more. They are also employed in renewable energy storage and backup power applications and also in industrial products such as robotics equipment. The end products are characterized by high energy density and promptness of operations and are widely used in various electronic gadgets, automobiles and energy storage.
Ans- Do not discharge lithium-ion batteries to zero percent and charge them fully to maximize battery durability, use charge level between 20-80%. Using the original charger and do not charge the headphone for a longer period of time. Charge the battery at the right temperature – away from heat and sun exposure. Do not use it where high band width or high performance demands are required. If devices are not in use for long time, they should be charged to around 50% and the firmware of the device should be updated frequently.
Ans- Indeed, majority of current laptops have lithium-ion battery as this type has high energy density per unit weight, fairly durable. These batteries offer power delivery, convenience of charge, and higher utilization time which makes these appealing for power driven items like pills. Some newer models even use lithium-polymer batteries, a variation of the lithium-ion technology and thinner than the other three models.
Ans- Lithium-ion batteries have electrodes where cathodes – compounds with lithium – are coated on aluminum foil and anodes – graphite – coated on copper foil and they are separated by a layer of a porous material. The assembly is filled with a lithium-ion electrolyte, sealed, and further the assembly is subjected to the first cycle of charging which is known as formation. The primary purpose of quality control is to guarantee both performance, safety as well as reliability in the end product.